OR/14/048 Description of the batch experiments
Rochelle, C A, Purser, G, and Milodowski, A E. 2014. Results of laboratory carbonation experiments on NRVB cement. British Geological Survey Internal Report, OR/14/048. |
Cement samples
The larger cylinders of cement were removed from the Ca(OH)2-saturated water and sub-cored to produce samples of 25 mm diameter for the batch experiments. There were then accurately machined to a length of 50 mm.
Experimental equipment
Laboratory experiments were conducted within the Hydrothermal Laboratory of the British Geological Survey, Keyworth, UK. Prior to performing the experiments, it was necessary to consider the use of equipment that would perform well. Although dry CO2 is relatively inert, in the presence of water or NaCl solution it is much more reactive. Previous investigations within the BGS Hydrothermal Laboratory and other studies (e.g. Schremp and Roberson, 1975[1]) have shown that steel can corrode and standard O-ring seals can blister and fail. To minimise both corrosion and experimental failure, exposed surfaces were chosen so as to be as inert as practicable. Therefore, the pressure vessels were made of 316 stainless steel with wetted parts lined with PTFE (polytetrafluoroethene) ‘cups’, high pressure tubing was made of either 316 stainless steel or PEEK™ (polyetheretherketone), and O-ring seals were made of Viton®.
The batch equipment used is relatively simple and generally free from day-to-day maintenance. As a consequence, the vessels are well-suited for running over prolonged time periods. Indeed, similar equipment has also been used successfully in previous studies of CO2-water-rock reaction (e.g. Gunter et al., 1993[2]; Rochelle et al., 2004[3], 2006a[4]). A schematic diagram of the equipment is given in Figure 3.
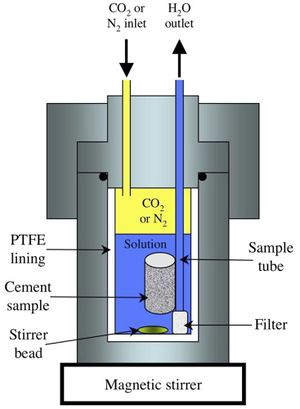
Assembly of the experiment involved first securing a small cylinder of cement (25 mm diameter and 50 mm long, approximately 40 g in weight) to the lower part of the sampling tube attached to the head of the vessel. This was positioned so that it would not touch the base of the vessel once assembled. Raising the cement off the bottom of the vessel was important during fluid extraction and sample depressurisation. At the end of the experiment depressurisation results in degassing of CO2 dissolved in the aqueous phase, and as a consequence the supersaturation of minerals such as carbonates. It is possible therefore, that if precipitation of these was rapid during the depressurisation process, then they might appear on the sample as an artefact and complicate subsequent interpretation. Although care was taken to remove as much fluid as possible prior to depressurisation (and hence reduce the potential for precipitation artefacts), experience has shown that CO2 break-through into the filter often results in a few millilitres of aqueous fluid remaining in the bottom of the vessel. By simply raising the cement sample above this remaining fluid, the potential for carbonate precipitation artefacts is greatly reduced.
Where used, a quantity (approximately 230 g) of cement porewater was placed into the PTFE liner of the vessel, together with a small magnetic stirrer bead. This amount of porewater was sufficient to cover the sample of cement. The porewaters used were one of; a synthetic ‘young’ cement porewater (rich in Na and K), a synthetic ‘young’ cement porewater with additional Cl, or a synthetic ‘evolved’ cement porewater (rich in Ca). The total volume of the solid and aqueous samples filled about 75% of the space within the vessels. For experiments involving both cement and porewater, the fluid:solid mass ratio was thus approximately 6:1. No porewater was added to the experiments reacting cement with dry gases.
Final assembly of the vessels involved a fresh O-ring being inserted into its groove in the head of the vessel, and the lid securely fastened down. The vessels were then placed into either a LMS thermostatically-controlled incubator for experiments at 20°C, or a Gallenkamp Plus2 oven for experiments at 40°C (both accurate to better than ± 0.5°C) and connected to the appropriate pressure line (Figures 4 and 5).
The CO2 and N2 were supplied to the reactors from ISCO 500D syringe pumps running in ‘constant pressure’ mode. The computerised controller allowed the pressure to be controlled to within 0.1 bar (0.01 MPa). Several vessels were connected to the same pressure lines to ensure they experienced identical conditions. Pressure connections were placed at the top of the vessels so that aqueous fluids (denser than high pressure N2 or CO2) could not move out of, or between, the vessels.
The vessels pressurised with CO2 represented the ‘reactive cases’ and those pressurised with N2 the ‘non-reactive cases’. This facilitated discrimination between reactions purely due to CO2, and artefacts that might be introduced by the nature/arrangement of the experiments.
Good mixing of the CO2 and synthetic porewater was achieved via the stirrer bead in each vessel. Although the base of the stainless steel pressure vessels was in the order of 1–1.5 cm thick, it still allowed for good ‘coupling’ between a magnetic stirrer and the stirrer bead. The vessels were stirred for several short periods each day — two minutes of stirring were used every 4 hours, which was controlled via an electronic time switch. Previous studies (Toews et al., 1995[5]) indicate that stable CO2 concentrations can be obtained in high pressure water-CO2 experiments within timescales as short as 30 minutes, though slightly longer timescales of just a few hours may be more realistic (Ellis and Golding, 1963[6]; Stewart and Munjal, 1970[7]; Czernichowski-Lauriol et al., 1996[8]). However, given the relatively long duration of the batch experiments (i.e. several weeks) and the relatively frequent stirring, it is reasonable to assume that the aqueous fluids within them were saturated with CO2 at the pressure and temperature of the experiments. The batch experiments were run under a range of conditions that are thought to be broadly representative of all possible future repository conditions at depths of 400 m and 800 m (Figure 6):
- 20°C and 80 bar pressure [liquid CO2 stable]
- 40°C and 40 bar pressure [gaseous CO2 stable]
- 40°C and 80 bar pressure [supercritical CO2 stable]
We acknowledge however, that of this selection, (2) is by far the most likely, and were the conditions under which flow experiments were also conducted (see Purser et al., 2013[9]). Conditions in (1) and (3) would require high CO2 production rates, which may be unlikely. That said, running experiments under these conditions would enhance reaction, and place limits on maximum amounts of carbonation. Also, if reactions mechanisms appear similar for gaseous, liquid and supercritical CO2, then that will provide robust evidence for a good understanding of cement carbonation over a wide range of conditions.
The other possible set of conditions would have been 20°C and 40 bar. However, as this would have also contained CO2 in its gaseous state (as per [2] above) and was relatively close to the liquid/gas phase boundary (Figure 6), it was decided not to run experiments under these set of conditions.
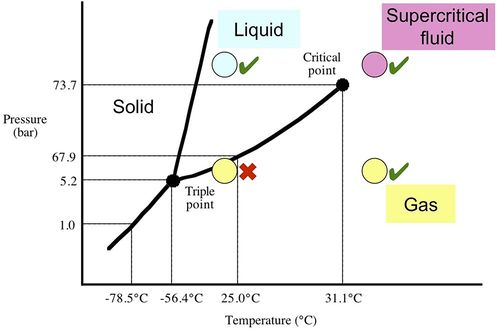
The above conditions were mainly used in shorter (10–40 day) experiments to assess the effects of gaseous/liquid/supercritical CO2 on the cement. Given the 2 types of porewater, some experiments being dry, and two gases, this gave a total of six experiments per set of conditions. However, a further six experiments were also run over longer timescales (12 months) to assess the maximum degree of reaction over as long a time as practicable within the work programme. The matrix of experiments is as detailed in Table 2.
At the end of the experiments sampling of the aqueous phase was carried out via a PEEK™ dip tube (with a 20 µm pore size polypropylene filter at the end), which ran to the base of the PTFE liner. Fluid samples were extracted whilst the reactor was still under run conditions, pressure being maintained through the injection of extra CO2 into the headspace of the vessel. The vessel was then depressurised, dismantled and the cement sample extracted.
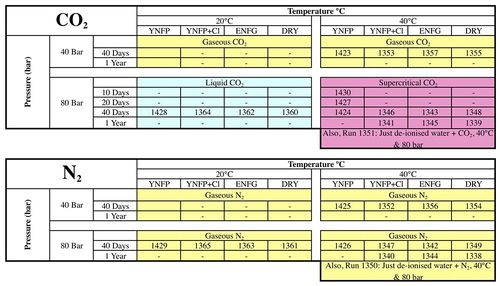
References
- ↑ SCHREMP, F W, and ROBERSON, G R. 1975. Effect of supercritical carbon dioxide (CO2) on construction materials. Soc. of Petroleum Engineers Journal, June edition, p.227–233.
- ↑ GUNTER, W D, PERKINS, E H, BACHU, S, LAW, D, WIWCHAR, B, ZHOU, Z, and MCCANN, T J, 1993. Aquifer disposal of CO2-rich gases. Alberta Research Council report, C-1993-5.
- ↑ ROCHELLE, C A, PEARCE, J M, BATEMAN, K, BIRCHALL, D J, CHARLTON, B D, REEDER, S, SHAW, R A, TAYLOR, H, and TURNER, G. 2004. Geochemical interactions between supercritical CO2 and borehole cements used at the Weyburn oilfield. British Geological Survey Commissioned Report, CR/04/009, 22p.
- ↑ ROCHELLE, C A, BATEMAN, K, MILODOWSKI, A E, KEMP, S J, and BIRCHALL, D. 2006. Geochemical interactions between CO2 and seals above the Utsira Formation: An experimental study. British Geological Survey Commissioned Report, CR/06/069. 86pp.
- ↑ TOEWS, K L, SHROLL, R M, and WAI, C M. 1995. pH-defining equilibrium between water and supercritical CO2. Influence on SFE of organics and metal chelates. Analytical Chemistry, 67, 4040–4043.
- ↑ ELLIS, A J, and GOLDING, R M. 1963. The solubility of carbon dioxide above 100°C in water and in sodium chloride solutions. American Journal of Science, 261, 47–60.
- ↑ STEWART, P B, and MUNJAL, P K. 1970. The solubility of carbon dioxide in pure water, synthetic sea water and synthetic sea-water concentrates at -5 to 25°C and 10 to 45 atm pressure. Journal of Chemical Engineering Data, 15(1), 67–71.
- ↑ CZERNICHOWSKI-LAURIOL, I, SANJUAN, B, ROCHELLE, C, BATEMAN, K, PEARCE, J, and BLACKWELL, P. 1996. Area 5: Inorganic Geochemistry, Chapter 7 in ‘The underground disposal of carbon dioxide’ (S Holloway ed.). Final report for the CEC, contract number JOU2-CT92-0031. Published by the British Geological Survey.
- ↑ PURSER, G, MILODOWSKI, A E, HARRINGTON, J F, ROCHELLE, C A, BUTCHER, A, and Wagner, D. 2013. Modification to the flow properties of repository cement as a result of carbonation. Procedia Earth and Planetary Science, 7, 701–704.